5S Examples – How NASA and others apply Lean
Ever noticed 5S examples outside of a factory? Not just the NASA is known for a good 5S approach in their space shuttle program. Let’s think of existing examples to learn from. 5S is an approach to achieve a structured and standardized environment whether inside a production plant or anywhere where quick and organized actions are required. In order to get there this approach is structured by the five terms sort, set in order, shine, standardization and sustain. Each step contains actions to improve and standardize your factory more and more – with a certain focus on people and organizations.
As tons of instructions and details about the 5S approach is available for free on the web we will not focus on that in this article. Let us talk about the more interesting aspect: 5S examples outside a factory.
5S Examples
Space Shuttle
Did you know that 5S takes a major role in the NASA space shuttle and Apollo missions to the moon? A key element is to sustain defined standards. In order to do so the human factor plays a central role. Especially when the whole success of a mission is depending on people. Therefor the NASA not just defined standards, routines and checklists but also trained the staff to respect them in every detail.
Fire Truck
Fire fighters have to react as quickly as possible to prevent further damage in case of a fire. For this reason, each action has to be as precise and fast as possible. When watching a fire truck very carefully you will recognize how accurate each device and tool is placed according to its probability to be needed. Just as we do inside our factory.
Emergency Cases
Almost each train or bus is equipped with a certain kind of hammer to break the glass in case of an accident. Not randomly that device is placed almost at the same spot all around the world. As emergency cases require quick actions and tools to be 100 % available it is even more important to take care of 5S.
Hospitals
As we already spoke about emergency cases same also applies to hospitals. As staff and shifts rotates more often than in other environments it becomes more important that each workplace is structured in a fully standardized and lean way. Not just actions like reanimation require 100 % fitting handling steps, also medicines and tools have to be named and located in a way each doctor can work with right off.

Title Image by Alan Freed / Shutterstock.com
Tags In
A Workshop Training Kit
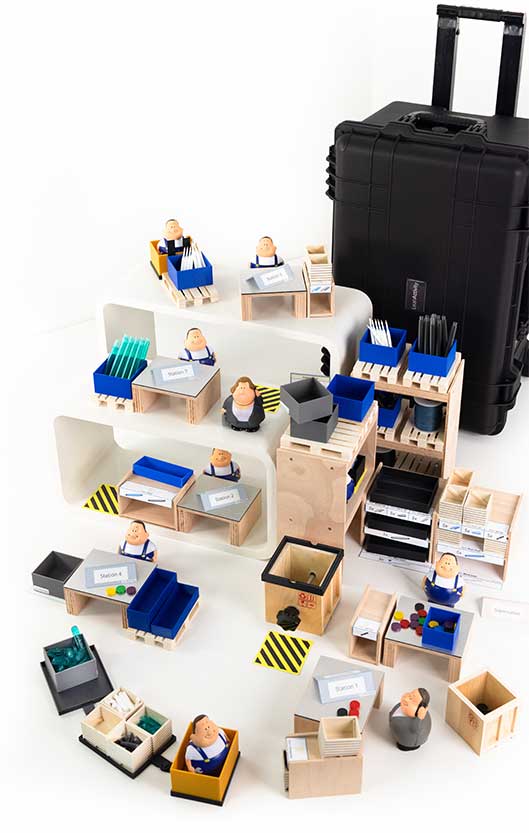